Component optimisation in the logistics department of Würth Industrie Service
Cost saving by means of component optimisation in robots
Since a robot in the logistics department of Würth Industrie Service repeatedly experienced defects in the mounting of a light plate, the experts from the CPS®WAM division carried out a topology optimisation and used additive manufacturing technologies to develop a lightweight alternative that creates considerable time and cost savings.
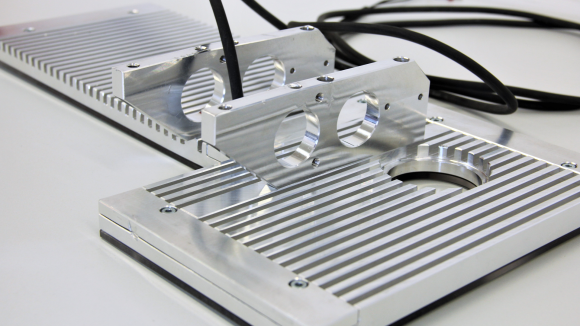
Initial situation
In the logistics centre at Würth Industrie Service, robots sort small load carriers, which are picked from the high-rack storage for shipping to the customer on pallets. For the recognition of goods, there is a light panel on the arm of the robot that is fastened with an aluminium fixation. The automatic exchange of the gripper arm for various bin sizes again and again leads to damaging the aluminium fixation of the light panel, thus requiring an exchange of the light panel. Due to the components used, the light panel system is sensitive, expensive to manufacture and is characterised by a high installation effort and long delivery times in case of repair. An improved design was created to reduce component costs, repair expenses and downtime, and successfully utilise the advantages of lightweight design for the dynamic load cases.
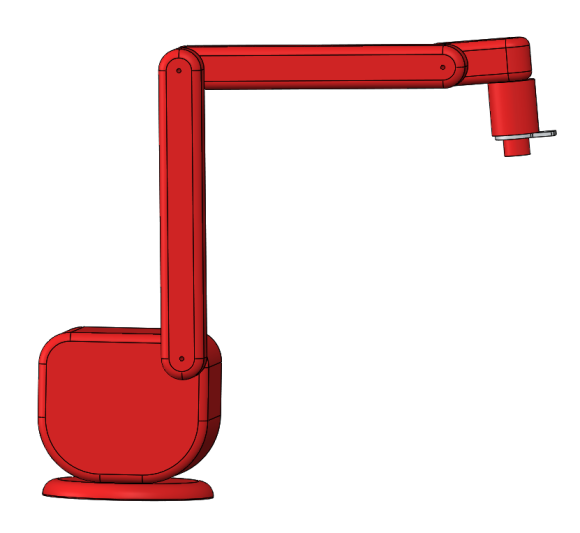
Actual analysis and multi-body simulation
In the following project flow, the dimensions and masses of individual components were determined, the movements of robots were analysed and a digital twin was designed. It was then possible to conduct a structural analysis with the collected data. With the help of the digital twin, we could identify how the acting forces in form of acceleration forces could impact the components of the robot, and which inner component tensions and component deformations could occur as a result.
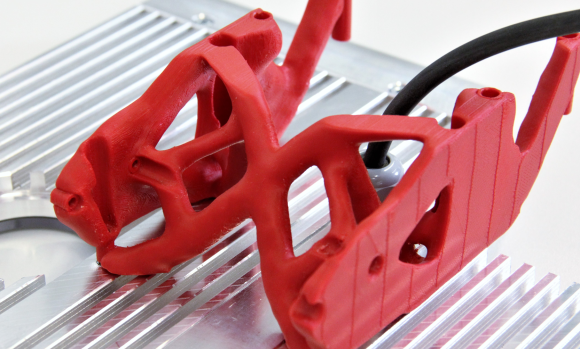
Topology optimisation – holder
The multi-body simulation thus generated forms the basis for creating a topology-optimised holder in the next step. This holder should achieve an optimised strength for the application, an improved design and thus a greater compatibility of the individual operations of the gripper change. The result of the project is a structural component optimised for lightweight design, which has a mass of approx. 87% of the original structural component but still withstands the acting forces. In event of a problem during a gripper change, a predetermined breaking point adapted to the application has been implemented in the holder. As a result, there is no need to exchange the whole structural component in the event of repair in the future, but only replace the relevant individual part.
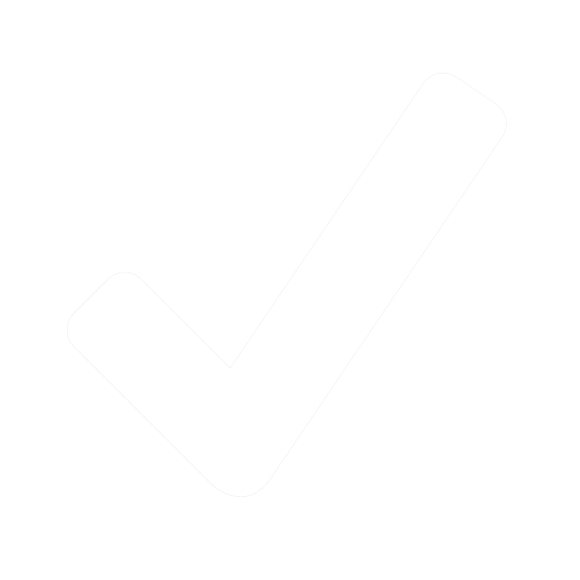
Factors of success:
In addition to reduced downtimes and repair times, the efficiently streamlined design has the potential to save costs, accounting to approx. 94% of the annual repair costs. Thus, the lightweight design not only improved the product design, but also resulted in overall optimisation – technologically, economically and ecologically.
Additional information
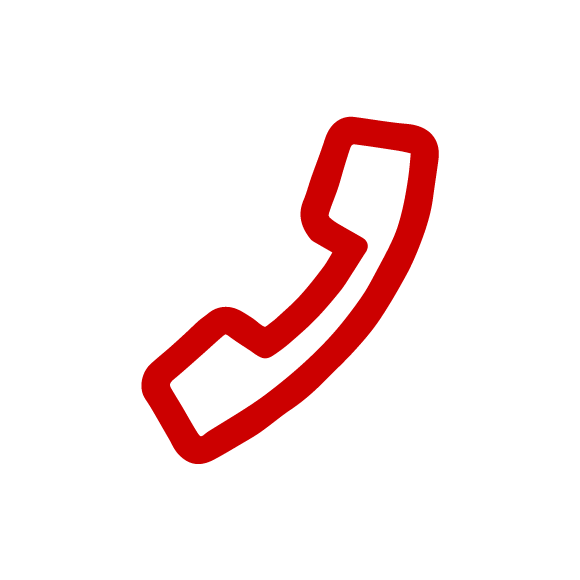
Contact
We are here for you!
Please contact us by telephone +49 7931 91 3972 or
via E-Mail under additivemanufacturing@wuerth-industrie.com.
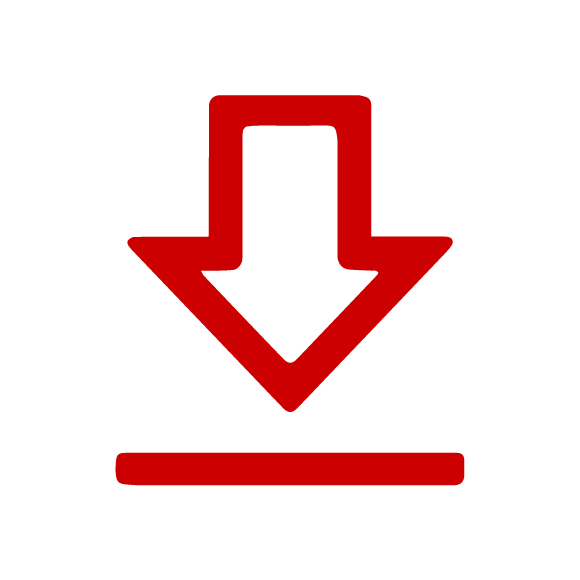
Websites can save or retrieve information in your browser in the form of Cookies. This may be anonymous statistical data, information about you, your settings or devices used, in order to enable a personalised web experience or so that the website works in the way you are expecting it to.
We respect your right to protection of your data. You can therefore decide not to accept certain types of Cookies. For an overview and the settings for the Cookies which we use, please see here. You can change these settings at any time, by invoking our Data protection declaration.
By saving, you confirm that you have understood the settings specified for Cookies and that you agree with them.
The Würth Industrie Service GmbH & Co. KG collects and processes the personal data provided in the form in order to process the requested request for you. Please note the mandatory fields in the forms. The legal basis for this processing, the absolutely necessary data, is Art. 6 para. 1 lit. b DSGVO, implementation of a pre-contractual measure. The processing of data voluntarily provided by you is carried out on the basis of Art. 6 para. 1 lit. f DSGVO. Thereafter, processing is permissible which is necessary to safeguard our legitimate interests. Our legitimate interest is to have contact with you, our customers, to improve our consulting quality and to be able to contact you more easily in case of possible queries. The data collected will only be stored by us for as long as is necessary to process your enquiry and to contact you. They are then deleted.
Supplementary data protection information, in particular regarding your rights to information, correction, deletion, restriction of processing, objection and complaint, can be found in our data protection declaration.